Download PDF
Bob Dunn says the new $140 million headquarters building for the Reinsurance Group of America (RGA) is “a game changer for St. Louis.”
“This is a project that RGA and St. Louis both really needed,” said Dunn, principal at Fox Architects, the interior architect on the RGA headquarters project. “There is nothing like it in Missouri,” he said. The 985,000-squarefoot project – 405,000-square-feet of office space and 580,000-square feet of parking – is the largest local project since Centene Plaza was completed in 2010, and the largest local headquarters project in the I-64 corridor in at least 20 years.
The St. Louis area has a reputation as a place where architectural designs follow trends started on the coasts 10 years before, Dunn said, but Jay Longo's design for RGA could help change that.
The new headquarters consists of two five-story, glass office buildings over a two-story, rock-skinned atrium and amenity base that includes a 20,000-square-foot, 500-seat cafeteria; a 10,000-square-foot training center; and a 7,500-square-foot fitness center. “The base represents RGA's core local knowledge. The towers are their global arms,” Dunn said. “Limestone represents the solid base RGA establishes in every market. The pattern of glass on the buildings reflects the mathematical work of the core business.”
Fox Architects has been RGA's architect since 1993, when General American spun the company off and federal regulators required them to have their own space. Dunn called the headquarters project “a once in a lifetime opportunity that doesn't usually go to a firm of 25 people.” Fox retained the interior portion of the project and helped the owner pick a design/build team for the core and shell.
Five design/build teams responded to RGA's invitation to propose a headquarters solution. Clayco partnered with Gensler, a global architecture firm with an office in Chicago. Among the other teams, Turner partnered with HOK and Paric partnered with Cannon Design. Clayco, which at the time was still based in St. Louis, “was the only one who did not use a local architect,” Dunn said.
"We looked at things and
questioned whether they
should be in the amenity
bar or a work bar,”
None of the design/build concepts hit it out of the park for RGA. Indeed, the buildings as built “do not look like any of the design/build presentations,” said Dunn, which is not unusual.
In a close race, other factors came into consideration. One architectural firm refused to modify their concept to accommodate RGA's desire for a later “Phase 2” expansion. That knocked them out of the running. RGA already had a local architect, Fox, and they wanted to have a local contractor. That hurt Turner. Of the three remaining teams, RGA selected Clayco as the best local contractor. The big difference? “Everyone else who proposed a Phase 2 treated it like a stepchild,” Dunn said.
Building Design
Because of the way the company is going to change, Fox and Gensler designed the building from the inside out.
Gensler came up with the idea of an amenity bar and two intersecting work bars. “We kept that mentality of calling it 'amenity' and 'work' bars as we moved forward. We looked at things and questioned whether they should be in the amenity bar or a work bar,” Dunn said.
Jay Longo was Gensler's project architect. As construction started, he left Gensler and set up his own firm, Longo Park. Before construction ended, Bob Clark, CEO of Clayco, had brought him into the Clayco fold to lead Forum Studio.
Fox Architects evaluated the size of work stations and informal areas, and analyzed RGA's population. The company had 753 employees in St. Louis and plans to quickly add 300 more. “Sixty percent of headquarters employees are Baby Boomers or Gen X, 40 percent are Millennials and Generation Y,” who have different expectations about work spaces. “A few years after they occupy the building, the proportions will flip. In 10 years, the Baby Boomers will be gone,” Dunn said.
All of that information factored into the planning of the interior, along with Fox's knowledge of RGA's work processes. “Our approach is about improving the business of our clients through space; not about how it looks. . . . Spaces should be designed according to how you operate,” Dunn said.
Company-wide and departmental conference rooms are placed to reduce disruptions due to people moving through work areas. Work stations have low walls to encourage quieter conversation. Every work station faces the corridor, which both elevates the privacy of information and reduces the chance of anyone startling anyone else. There is an extra chair for each body in RGA to enable anyone to have a private, oneon- one meeting at any time and to encourage people, for ergonomic reasons, to periodically get up from their desk chairs.
As the design moved through various iterations, Fox moved 50,000 square feet of space out of the amenity area and into the work bars, which increased potential occupancy from 1,280 to 1,450. Gensler then made the work bars cantilever more over the base. “That was the biggest impact we had (on Gensler's design),” Dunn said.
“Jay (Longo) always had a vision of what the exterior would look like, even though he showed RGA probably 30 different models,” said Dunn. One of the early design ideas was for a single, 10-story tower. “Where we ended up was spot on for RGA. The look is Gensler and Jay Longo. The length, width, the square footage in the base and the square footage in the towers, that is Fox,” said Dunn.
The facility was designed to cut energy use 25 percent compared to a 'typical' office building and achieve LEED (Leadership in Energy and Environmental Design) Gold certification from the U.S. Green Building Council. The stance of the building is tied to solar orientation to save energy. Low-e glass reduces solar heat gain. Energy efficient lighting is tied into the building automation system with occupancy sensors and daylight harvesting, but the latter can be overridden by the mechanical shade system, which is tied to the mechanical system by the same automation system, to keep cooling costs down.
"The facility was designed to cut energy
use 25 percent compared to a 'typical'
office building,"
Construction
Tom Sieckhaus, executive vice president, Clayco, said that the chief construction challenges were:
• building the two work bars (towers) with 40-foot cantilevers over the first floor, which required strategic sequencing of steel erection and concrete pours,
• the intertwining of the concrete garage with the structural systems for the office buildings,
• the 30-foot tie-back retaining wall at one end of the underground portion of the garage,
• the limestone rain-screen system, and
• investigating and designing the subgrade elevations for the garage to minimize rock excavation.
“The cantilevered features are unique,” he said. “The two work bars cantilever out 40 feet with composite metal panel soffits and there is a perimeter walkway below with a glass railing. It is a really cool design.”
Nathan Cook, Clayco project manager, said it was a challenge to sequence work to build the job as designed. “Typically, jobs are built a floor at a time. The cantilevers meant we couldn't do that,” he said. Steel k-braces provide lateral support in the office towers. The construction team could build only up to where the k-brace would be welded to the floor. Brace members would get welded to a gusset plate, which was welded to an embed plate.
“We built about two-thirds of a floor, then built about two thirds of the floor above it, and when the brace was welded to the floor we went back and built the last third. We needed things tied in on each floor before the brace, and that affected the concrete pours,” said Cook.
Weaver Steel Construction erected the steel structure. Partial floor assembly required more coordination and planning than typical full-floor construction. “On this building, steel had to be detailed and delivered in the order in which it was needed,” Cook said.
“We have expansion joints and columns
for the tower pass through the garage. It
made scheduling hard."
Ben Hur Hammerts (BHH) was the steel supplier. Clayco and BHH used a building information model to coordinated detailing and delivery.
After erecting the first floor, workers built four large, temporary shoring towers for the cantilevered section. After the concrete was poured, but before the glass curtain wall was installed, workers utilized hydraulic jacks to raise the cantilevered building section enough so that they could pull out the shoring. Then they measured how much the overhanging floors sagged. It was about one-eighth of an inch, Cook said. “That had to be done before the curtain wall went up, because the sag was enough it would have cracked the glass,” he said.
Permasteelisa fabricated and installed the curtain wall as fully unitized panels that interlocked during installation. They were able to glaze a full floor in only eight days.
The tower structures are integrated into the garage, which is unusual. “We have expansion joints and columns for the tower pass through the garage. It made scheduling hard. The garage had to be about 40 percent complete before we could start the tower structures,” Cook said.
Some of the structural complexity derived from the site. SCI Engineering performed a site exploration in January 1999, followed by a geotechnical study in June 2012.
“The site is partially on a bluff,” said Project Manager Shawnna Erter. “There is a limestone ledge that runs through a portion of the building, then there is a significant drop in rock elevation of about 60 feet. So you would hit rock in one part of the building footprint, but have 60 feet to go before hitting rock in the other part of the building. That creates a significant risk of structural settlement,” she said.
And, there are two types of rock, which have different load-bearing capacities. Part of the building is over limestone bedrock, which is hard, but another part is over shale, which is soft.
“Anytime you design with more than one type of foundation, it makes it complicated,” Erter said. “We could have said everything has to be drilled piers, but that would have made it ridiculously expensive. Instead, we worked with the structural engineer to come up with a system that works and is safe and is cost effective for the client,” she said.
Concrete Strategies formed and placed all the concrete, from a 30-foot tall tieback wall on the side of the garage near Swingley Road to the columns and floors of the garage to the columns and floors of the office buildings.
Heitkamp Masonry installed the limestone on the amenity base. “The stone is really a rain screen. There is no mortar, and it was a challenge to maintain the integrity of the weather barrier with the stone,” Cook said. The wall behind the stone was installed in layers: weather barrier, flashing, rigid insulation, then stone. The anchors for the stone were installed on top of the weather barrier, which in some parts was sprayed on and in other parts consisted of Carlisle 705 adhesive sheets. The problem was that in penetrating the weather barrier, the anchors for the stone provided a route for moisture to travel through the wall.
Heitkamp hung each piece of stone from anchors attached to the wall. They had to use larger, heavier anchors than they typically use in order to extend through the insulation, which was on the outside of the wall. “We had to do a very good job of waterproofing the anchors with sealant,” said Project Manager Art Siebert. “We looked at the system they (Carlisle and Gensler) wanted and figured out, with their approval, how to do it.”
As a rain screen system, each piece of stone was hung independently, which Siebert said is much more challenging than building a wall from the ground up with mortar. “We had 4,000 pieces of stone on the job and almost 50 percent were one of a kind,” he said.
*Originally published in the November-December 2014 Issue of St. Louis CNR Magazine
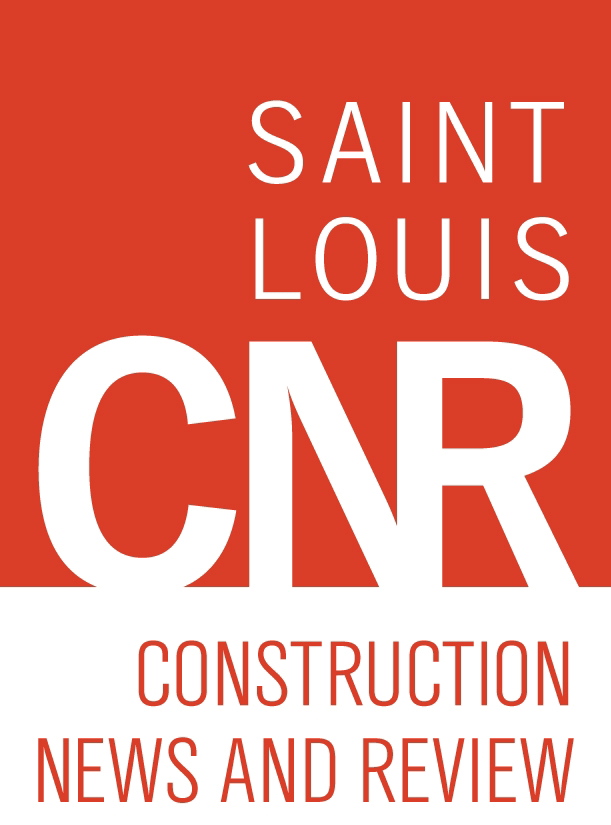